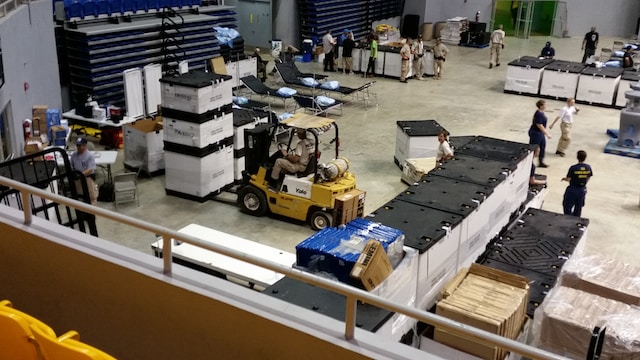
製造業の現場を見学する機会が多い中で、先日は海外(アジア)にも工場を展開する企業の担当者とお話しする機会がありました。そこで感じたことを、多少のステレオタイプも交えつつ、率直にお伝えしたいと思います。
かつては「Japan as Number One」でも今は?
かつて、日本の製造業は世界中から高く評価され、「Japan as Number One」と称される時代がありました。高品質で壊れにくい製品が日本の強みであり、一時は世界市場を席巻しました。しかし、数十年が経過し、製造業が「コモディティ化」する中で、製造のステージは海外、特にアジアへとシフトしています。
国内と海外に工場を持つ企業担当者からの話に戻りますが、国内工場は忙しくはあるものの苦戦している一方、海外工場は比較的順調とのことです。この違いにはいくつかの要因が考えられます。
生産性の違い
まず、日本国内市場の縮小が挙げられますが、それ以上に注目すべきは生産性の違いです。単純に考えても、雇用人数の差や人件費の違いが大きな影響を与えています。日本国内では、人(職人)に依存した製造が基本である一方、海外工場では、管理手法に基づいた効率的な生産が行われています。
日本の製造業の基本は品質第一ですが、これは品質至上主義とも言えます。一方で、海外では効率化を重視し、その上で品質を担保する手法が取られています。これにより、かつては不良が多いと言われた海外製品も、今では「効率化+品質」を実現しています。
こうした背景から、日本の製造業は過去の栄光やプライドから脱却できず、「品質重視」だけで「良いものさえ作れば売れる」という考えに固執してきたのかもしれません。その結果、効率化が後回しにされ、国内での生産性向上が遅れている現状が浮き彫りになります。
丸亀製麺の事例
具体的な事例として、丸亀製麺を挙げてみましょう。国内の店舗では、少数のスタッフが効率よく業務をこなしている一方、海外店舗では、スタッフの数が格段に多く、作業が細分化されています。これにより、人件費の高騰を招き、さらに自動化が進むという結果が生まれています。
このような違いを踏まえ、国内工場でも効率化のヒントを得られるかもしれません。品質至上主義の盲点に気づき、「品質&効率化」のバランスを取りながら、海外工場の成功事例を学び、取り入れることが求められます。
最後に、日本の製造業が生き残り、再編を果たすためには、国内外の良いところを取り入れたハイブリッド経営が鍵となるでしょう。品質と効率化の両方を重視した生産体制を目指すことで、持続可能な競争力を維持することができるはずです。